A webinar and virtual expo was organized on Advance Materials for Defence & Aerospace by Indian Military Review and Centre for Joint Warfare Studies (CENJOWS) on 9 Apr 2021. The event was conducted in five sessions in which the speakers from industry and armed forces, scientific community and academia, participated. The participants presented and discussed issues relating to special materials, alloys and composites used in aerospace, land and naval platforms, weapon systems like missiles, guns and naval warships. Separate sessions covered smart and future materials and additive manufacturing & 3D printing.
Inaugural Session
Opening Address. Welcoming all delegates, the Director of CENJOWS, Lt Gen Sunil Srivastava, explained that India imports nearly 37% of its requirements of special steel despite the fact that it is the second largest producer of steel. Similarly, it imports several nickel, cobalt and iron based super alloys for use in nuclear reactors, turbines, rocketry and so on. This has strategic implications as well as results in huge financial outgo which is avoidable if we innovate and develop our own manufacturing. The market of Advanced Materials has experienced exponential growth across the world. In India itself, it is growing at a CAGR of 4.5% during 2020-2025. India uses nearly 2 billion dollars of the critical materials annually. In particular, we need to work out short-term and long-term strategies to overcome constraints. It is not an impossible task since India has already displayed its ability to innovate and develop in space and nuclear technology which is at par with the developed countries.
Inaugural Address. Dr Satheesh Reddy, Chairman DRDO & Secretary Defence R&D underscored role of strategic materials in economic growth of the nation. He emphasized that since we lacked the technology to produce advanced composite materials, it was necessary to work out long-term plans for procuring the core materials. The process involved assessing own requirements of the specific materials, ie, how much raw material we hold in the country and how much more we need to import; thereafter, identify countries where it was available and then secure mining rights to source these materials through our indigenous companies for our industry. As regards the processing technology, it was essential to either develop it through own R&D or through partnership with foreign OEMs. He said that we also need to put in place appropriate infrastructure and machinery and finally, the product quality produced should match with the world standards. He listed some generic strategic materials/products like special steels, aluminum, tungsten, carbon fibres, additive manufacturing, semiconductors, silicon wafers, magnets etc. Lastly, he suggested that for synergy, all stake holders should join and follow a time bound strategy to achieve self-reliance.
Industry Perspective. Col KV Kuber, Director Defence & Aerospace, Ernst & Young gave the industry perspective and brought out that Indian industries were engaged in developing composite materials and BEML and Midhani have achieved significant success but still the range of products was small and volumes produced were low. Our industry should not only meet the domestic requirements but also generate capacities for exports.
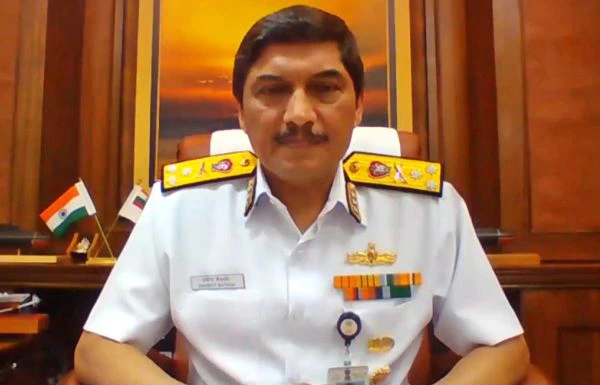
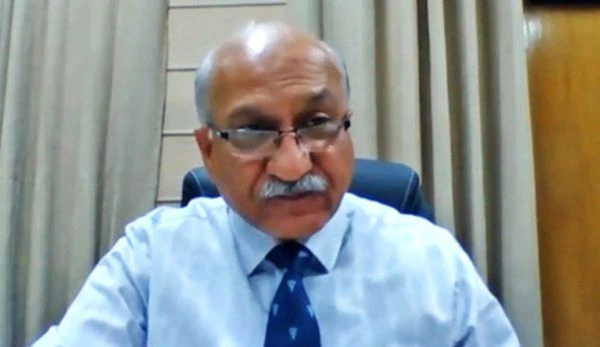
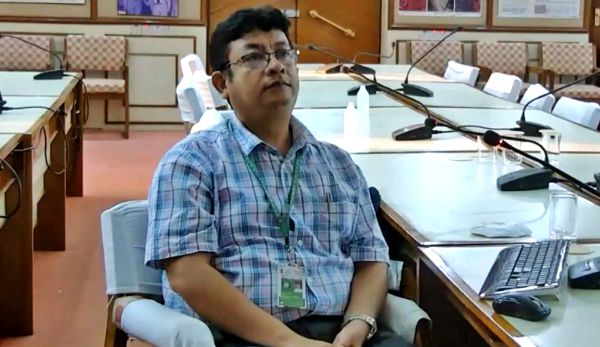
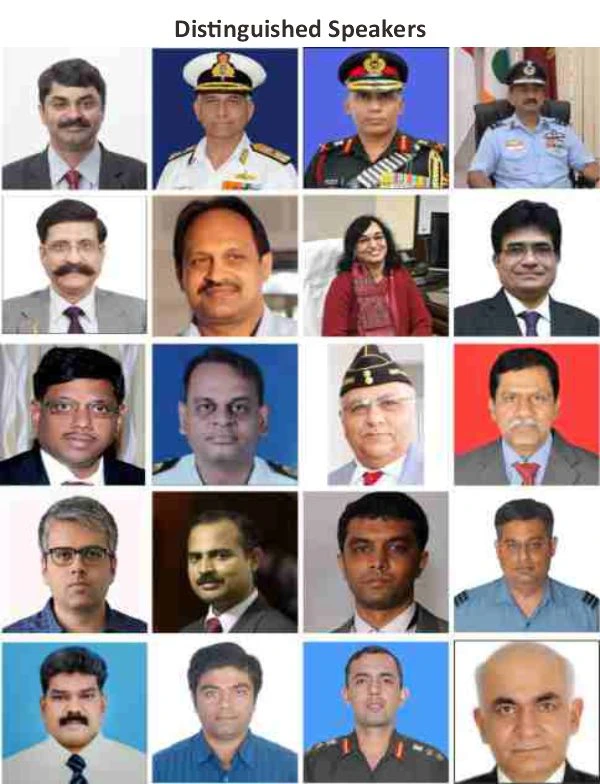
Key Issues Needing Attention
From the deliberations of the participants from DRDO, Industry and Services it was clear that Indian armed forces are already using numerous indigenous platforms and weapons with indigenously developed composite materials, eg, LCA, AEW&C, Astra, ASAT, BrahMos, Nag ATGM, Arjun MBT Mk 1A, MPR, LLTR, etc, to name a few. Still, a lot needs to be done as domestic consumption of composites was far less when compared, say with China and USA. Just 0.3 kg against 2.5 kg in China and 11 kg in US. The reason was both lack of awareness and technology. The webinar brought into focus some important issues which are briefly explained below: –
• In spite of the tremendous progress, Indian Industry still faces technological challenges in development of composite material in India.
• Indigenous materials are not accepted by the manufacturing industry for several reasons e.g. uncertainty of the specifications, non-availability of appropriate technology and higher cost of the materials.
• Virtual designing of composite materials is in vogue in foreign Industry (e.g., Siemens)
• Indian Composites industry is less R/D intensive and poor IP protected.
• The quality assurance process of DGQA is time consuming and follows archaic practices.
• This single-shell molded structures provide higher strength at lower weight complex shapes hence, should be the focus area of the industry.
• Certification of the composite materials is problem area.
• Developing indigenous capability in semiconductors remains a challenge.
• Indian Industry has limited capacity to produce metal and alloy powder for additive manufacturing and molding of small components.
• Can additive manufacturing be taken up in the military at the field level to avoid disruption/delays in the supply chain?
• The foreign private industry uses virtual tools like Digital image correlation and Virtual simulation. This can help in structure designing, quality and validation of the product before actual product is manufactured.
Commentary
Research & Development. The government of India, in its DPP 2020, has tasked DRDO to work out a strategy in consultation with the Services and collaboration with other scientific and industrial establishments to set up missions for growth in select areas including composite materials which must be pursued vigorously.
Spurred by Make in India, there is a robust demand of composites in India which is rising with CAGR of 8.2% annually. This has given impetus to R&D and indigenous production. Speakers from Midhani and BEML have claimed that their company have several patents. This situation must also exist in the
private industry. Foreign OEM’s are not likely to share the technology which necessarily will have to be developed locally.
Quality Consciousness. There is lack of quality consciousness amongst the medium and small industry. Midhani and DMRL in the government and several private industries have developed multitude of indigenous raw materials to preclude dependence on OEMs. They should transfer the indigenously developed technology to the domestic enterprises to improve the quality of their products for the defence sector. Greater volume of production of the raw materials will reduce the costs of the materials.
Indian industry should adopt new modelling technology which besides saving time and effort will result in better quality product.
Though Regulatory agency ensures maintaining of robust quality standards, its methods are antique. It must make use of virtual processes for evaluation.
Standards and Certification. Considering the stated advantages, DRDO should examine the manufacturing process.
The composite has to conform to the standards. It is the responsibility of the OEM to get the product certified. The challenge is greater in indigenous production of import substitute products.
Indigenous Development and Production. Semiconductors have wide applications and used practically in every electronic circuitry/gadget used in defence, (eg telecommunication, transportation, entertainment etc). Our own domestic industry is making strides but, still we are way behind and import nearly 60-70% of our requirement. To encourage indigenous production, the production policy allows 100% FDI in the semi-conductor to attract investments including from Original Equipment Manufacturers (OEMs).
80% of metal powders used in the powder metallurgy industry are Iron based powders while 20 %are non-ferrous. India solely depends on imports of iron powders. The drawback of not having indigenous production and the resultant dependence on imports makes for an expensive proposition and depletes market competitiveness. International Advanced Research Centre for Powder Metallurgy and New Materials (ARCI) of Government of India is involved in research of metal powders and transfers technology to the industry to take it forward.
Additive Manufacturing. Additive manufacturing technology allows manufacturers to print entire components with precise tolerances. Thereby, improving part reliability and product quality. It came out clearly in the webinar that only small components can be manufactured with this technique. Secondly, large infrastructure is needed which cannot be provided at the field units however, it can be attempted at the base workshops/ base repair depots to manufacture the critical parts.
DRDO and its related industry could upscale their’ designing, development and manufacturing with these new techniques.
Recommendations
On Self-Reliance. Developing own raw material is a key to self-reliance. Disruption in global supply chain will always remain a possibility. Atmanirbharta is the key to avoid it.
Work out short term (5 years) and long-term (15 years) strategies to overcome constraints in advance materials. It is not an impossible task since India has already displayed its ability to innovate and develop in space and nuclear and space technologies which are at par with the developed countries.
Indian R&D institutions like International Advanced Research Centre for Powder Metallurgy and New Materials (ARCI), DMRL and Midhani should transfer technology to Indian industries involved in development composites so that do not face constrains such as non- acceptance of the indigenous materials because of uncertainty of its specification, non-availability of the technology and certification.
Research & Development. Secure the processing technology either through own R&D or through partnership with Foreign OEMs. We also need to put in place appropriate infrastructure and machinery.
Because of the need for huge infrastructure and machinery the Additive/30 printing of the critical/non-critical components can be attempted at the BRDs and Base repair depots only. The low volume of production and small size of components are the key constraint. Whether it can remove the supply chain delays is questionable.
Quality Control. Use of virtual tools like Digital image correlation and Virtual simulation can help in structure designing, their quality and validation of the product before actual product be taken up for adoption by DRDO and private industry.
Quality Assurance/ certification agency should explore digital/ virtual evaluation to cut down the time lag in their process of certification.
Conclusion
The webinar on advance materials gave good insight of the issues involved in production of the advance materials, its relevance for Atmanirbharta and role in uplifting the economy of the nation. Self-reliance in Advance materials will give major boost particularly to our defence sector and Indiacould become an export market. Based on the talks from the eminent speakers some doable recommendations have been made for the consideration of the related agencies.
SPEAKERS AND SUBJECTS
SESSION 1 – INAUGURAL SESSION
Welcome Address. Lt Gen Sunil Srivastava, AVSM, VSM**, Retd, Director, Centre for Joint Warfare Studies
Inaugural Address. Dr Satheesh Reddy, Chairman DRDO
Industry Perspective. Col KV Kuber, Retd, Director Defence, Ernst & Young.
SESSION 2 -AEROSPACE MATERIALS
Chairperson: Air Mshl SP Wagle, VM, DCIDS (PP & FD), VM, HQ IDS
Mr Umashankar G, Dassault Systemes. “Multiscale Material Modelling for Composite Structure.”
Mr TC Subba Reddy, Gp Director (Composites) ADA. “Challenges in designing the LCA Tejas.”
Dr Vijay Petley, Sc F, GTRE. “Special materials for aero engines.”
Mr Lalan Singh, Regional Technical Manager, Ansys.”Digitize Materials Knowledge with Ansys.”
Dr N Eswara Prasad, OS/Sc H & Director, DMSRDE. “Adv Materials, Products & Systems”
SESSION 3 – MATERIALS FOR MISSILES, ARTY GUNS AND NAVAL WARSHIPS
Special Talk: Dr Madhusudan Reddy, OS & Director DMRL, DRDO.
Chairman: Dr. Seema Vinayak, Scientist ‘H’, Director Solid State Physics Lab
Mr SK Jha, CMD, MIDHANI. “Key challenges in meeting the requirements of advanced materials for defence & aerospace in India”
Mr R Jaiganesh, Director RDAQA (GW&M). “Specifications and standards, QA and certification.”
Cmde Vineet Tiwari, Cmde (Naval Design), “Advanced Materials for naval shipbuilding.”
Mr Dinesh Tallur, Head, Portfolio Devp, Siemens Industry Software India. “Siemens Multimechanics – Multiscale Material Modeling for Characterization
SESSION 4: ADDITIVE MANUFACTURING & 3D PRINTING
Chairman: Lt Gen Sanjay Verma, PVSM, AVSM, VSM**, Retd, Consultant DRDO & former DG Capability Development
Wg Cdr Pratush Anand, 11 BRD, IAF. “Challenges in indigenisation of Su-30 MKI spares”.
Dr. Dwarak Krishnan, Dassault Systemes. “Design and Simulate Additive Manufacturing: Micro to Macroscale.”
Mr Kumarswamy S, Director – Testing Solutions & Engineering Consulting. “Characterizing materials and structures with Digital Image Correlation”
SESSION 5 – SMART AND FUTURE MATERIALS
Chairman: Cdr (Dr) Bhushan Dewan, Retd, M.Tech (Electronics & Telecom Engg) IIT-D, former VP TCS.
Dr M Manivel Raja, Sc F & Group Head, Advanced Magnetic Group, DMRL, DRDO. “Smart Materials for Future Military Electronics Applications”
Col Rajiv Ahlawat, Col PP (Engrs), Army Design Bureau. “Advance materials and 3D printing applications for Indian Army.”
Closing Remarks. Lt Gen Sunil Srivastava, AVSM, VSM**, Retd, Director CENJOWS
Maj Gen Ravi Arora, Retd, Chief Editor, Indian Military Review.